Having to enter data manually into IFS in the production department, lost inbound and outbound operation tracking sheets, human error while recording data — these were all problems Aunde was trying to address. The solution proved to be Novacura Flow, a platform that enabled production optimization with low-code platforms.
Only 5% of Aunde staff are office workers; the remaining 95% are directly engaged in manufacturing textiles and knitted fabrics that are sold to worldwide automotive brands for use in cars. It was the former who ended up fully responsible for operating the IFS system after it was rolled out. There were unsuccessful attempts to extend the roll-out to the production department — but the system proved to be too complicated to use and the production staff continued to record information by hand on sheets of paper. This showed a clear need for workflow optimization for office workers in manufacturing.
The introduction of IFS Applications was a major step in our company. Our processes really did begin to run more efficiently and information flow was smoother (...)
Aunde exemplified a company where existing management support systems had exhausted their capabilities and were not keeping up with the dynamics of its emerging processes, particularly in the context of digital transformation in the automotive supply chain.
We wanted to put the office staff to better use at tasks that involve more creativity than punching data into the system, for example, production planning, creation of new business strategies, looking for savings (...)
Great needs
Aunde employs 600 people who work on a surface area of over 20,000 m2, divided between two locations. The main problem was the ‘overwhelming paperwork’ and the need to monitor two locations. Despite the facilities introduced by IFS, many processes were still being handled manually. A lack of coordination between the office team, who worked daily from 8 a.m. to 4 p.m., and the production department, who operated on a two- or even three-shift schedule, was leading all transactions carried out in the company to be entered into the system with considerable delay. Tracking sheets would often get misplaced, and production information written down by office staff contained errors.
Aunde needed new tools — flexible and quick to implement and modify — tools that would help free office workers from tasks that can be performed faster and more precisely by machines, e.g. scanners. They turned to Novacura Flow, a low-code for technical textile manufacturing solution that provided exactly this level of agility.
Over time, however, the IFS system turned out to be too fundamental and the needs to develop IT systems appeared almost immediately in line with the development of the company.
The company was also concerned about improving communication between employees, thanks to which it would be able to avoid delays and delegate responsibilities more easily, for instance during holidays. All of this had to be integrated with the existing ERP system.
Therefore, the same cooperation model that had been implemented in TRI Poland was applied in Aunde.
Work on improving all logistics and production processes began in December 2014. Novacura Flow is now operating in materials logistics — this concerns not only inbound operations and transfers as well as outbound deliveries to production or customers, but also pallet handling and cooperation service transactions.
We wanted to put the office staff to better use at tasks that involve more creativity than punching data into the system, for example, production planning, creation of new business strategies, looking for savings (...)
The Aunde considered success of this implementation as a large part that came from a very good relationship with the customer. Novacura Flow has allowed for basic processes to be rapidly implemented and then improved based on user feedback. The work went very smoothly during the implementation Aunde representatives were open to suggestions from our consultants.
Good practices
Novacura’s specialists won Aunde representatives over with their solution by showing how it had filled the gaps in the current ERP systems used by TRI Poland. The company observed how Novacura Flow worked ‘in vivo’.
Just like us, TRI has a difficult technological process. We saw first-hand at their company, however, that it could all be well planned and sorted out. During the reference visit we were impressed by the contact between Novacura and TRI — there was none of the distance we have previously experienced in cooperation with other suppliers.
Cooperation with prospects for the future
Today, Aunde has 40 licences for Novacura Flow and is regularly supported by specialists from Cracow, but day by day its small internal IT department is doing a better and better job of modelling processes and adapting them to the dynamically changing conditions in the company.
During a conference organized by Novacura, we explored other possibilities of Flow and now we want to learn how to put them into practice
Aunde designs and produces technical fabrics, textile and leather car seat covers, technical springs, complete seats, foam parts, and composite interiors and elements for worldwide automotive manufacturers
We have plenty of new ideas about how to develop our processes. With the help of Novacura specialists and our IT department, which knows the needs of the company best, we will certainly better adapt our processes to the requirements of a dynamically changing reality.
Thanks to the introduced improvements, production — the company’s primary focus — can proceed much more efficiently, and the small number of office workers can finally concentrate on optimization, strategy development, and cost reduction, supported by process automation for industrial manufacturing tools that scale with business needs.
FAQ
How to reduce manual data entry in manufacturing?
To reduce manual data entry in manufacturing, companies should adopt process automation for industrial manufacturing using flexible and user-friendly platforms like Novacura Flow. Aunde successfully replaced paper-based tracking and manual ERP input by introducing barcode scanners and automated workflows built on a low-code platform, significantly minimizing human error and administrative workload.
What is the best low-code platform for textile manufacturers?
For companies in the textile sector, Novacura Flow stands out as one of the best low-code platforms for textile manufacturers. It allowed Aunde, a major producer of technical textiles and automotive seat components, to modernize its logistics and production processes without overhauling its ERP system. The platform’s adaptability and speed of deployment proved essential in meeting the industry’s dynamic needs.
How to integrate ERP with low-code in a production company?
Integration of ERP with low-code tools requires choosing a platform that supports seamless communication between existing systems and new workflows. At Aunde, Novacura Flow enabled ERP integration for textile manufacturers by extending IFS capabilities with user-friendly interfaces and automation layers. This helped synchronize production and office operations, reduce delays, and enhance data accuracy.
How do automotive suppliers digitalize internal workflows?
Automotive suppliers can digitalize internal workflows by leveraging low-code for automotive components production. Aunde used Novacura Flow to bridge the gap between office teams and production staff, automate data handling, and improve interdepartmental communication. This kind of digital transformation in the automotive supply chain enables faster, error-free operations and empowers small IT teams to manage ongoing optimization internally.
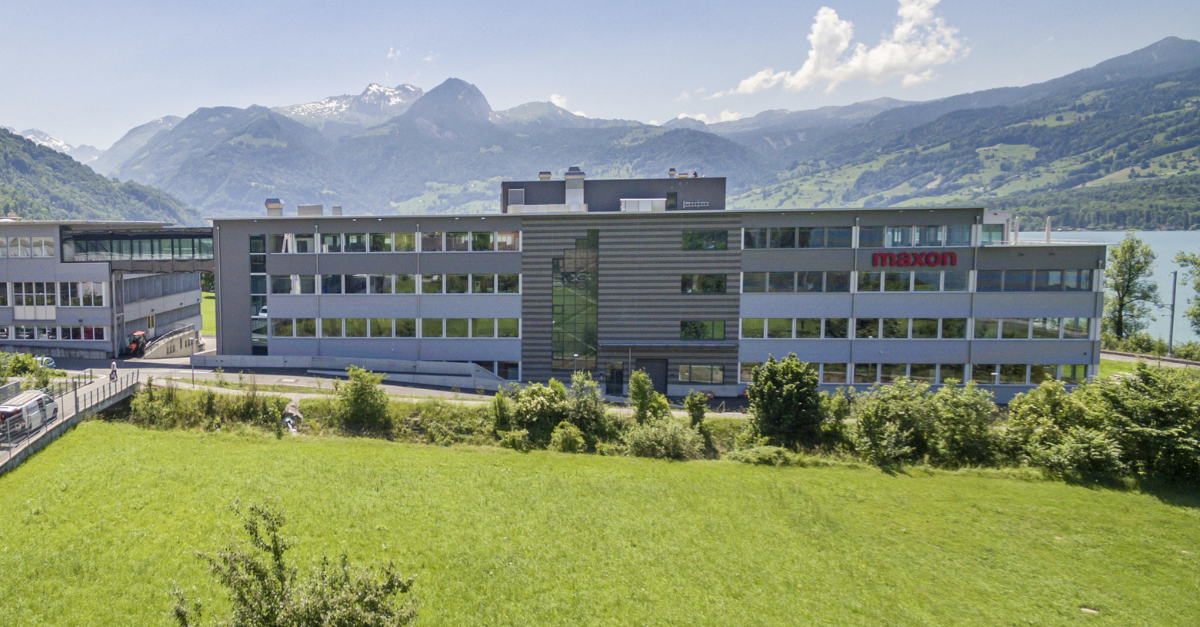
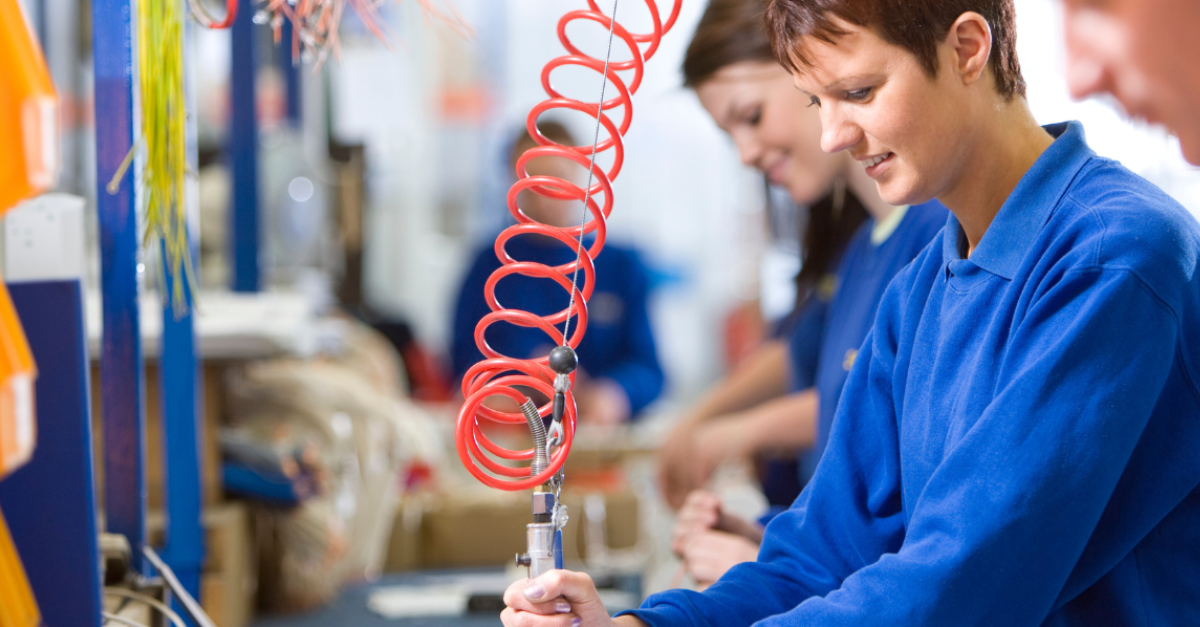
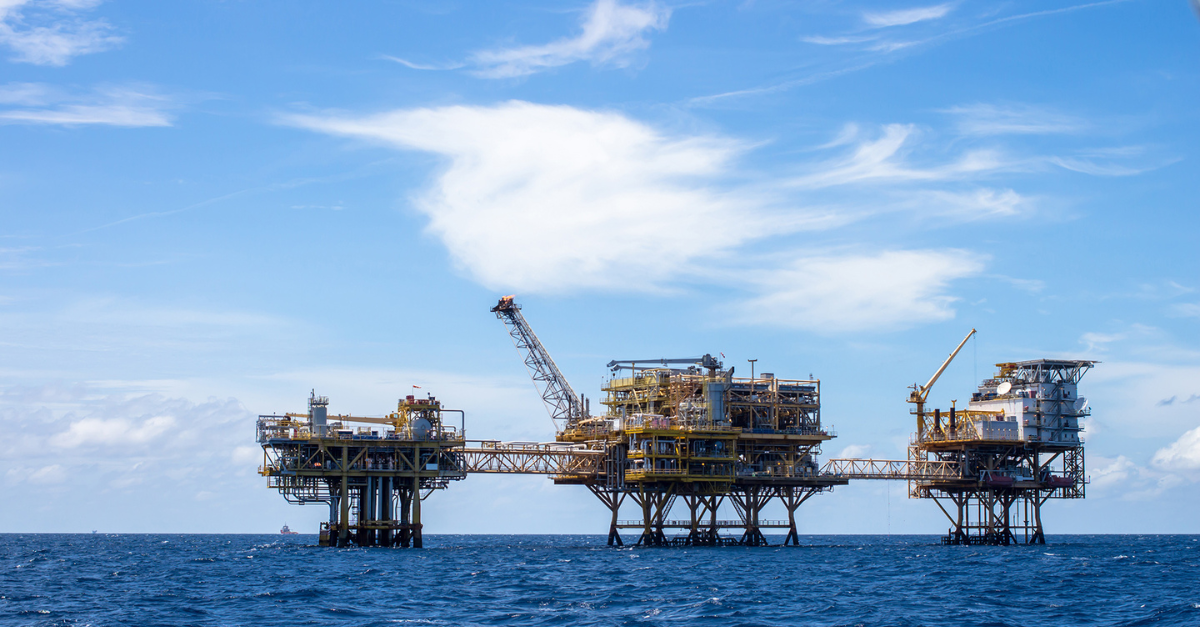
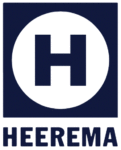