Streamline your manufacturing processes with dozens of applications dedicated to your ERP system
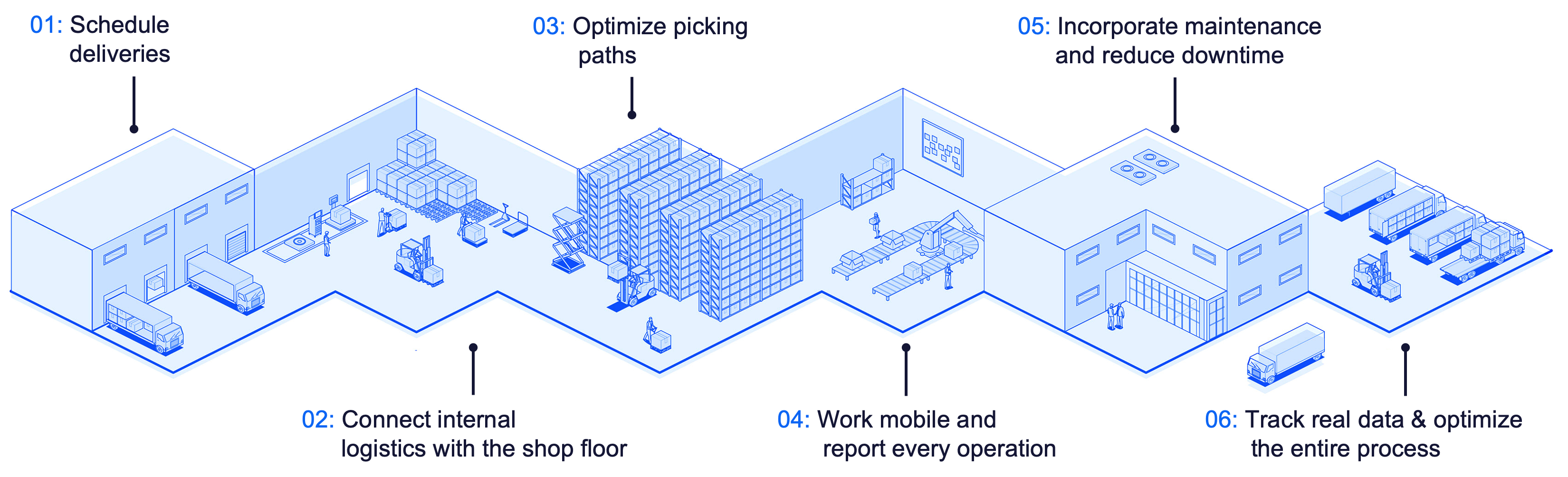
Manufacturing app advantages:
01. Schedule deliveries
With Novacura Flow applications, you can plan material requisitions based on your production plans and current stock levels. It is possible because these areas are supported by one integrated solution.
You can use B2B Portal to confirm the delivery schedule with your suppliers and – finally – book a suitable time-slot for unloading!
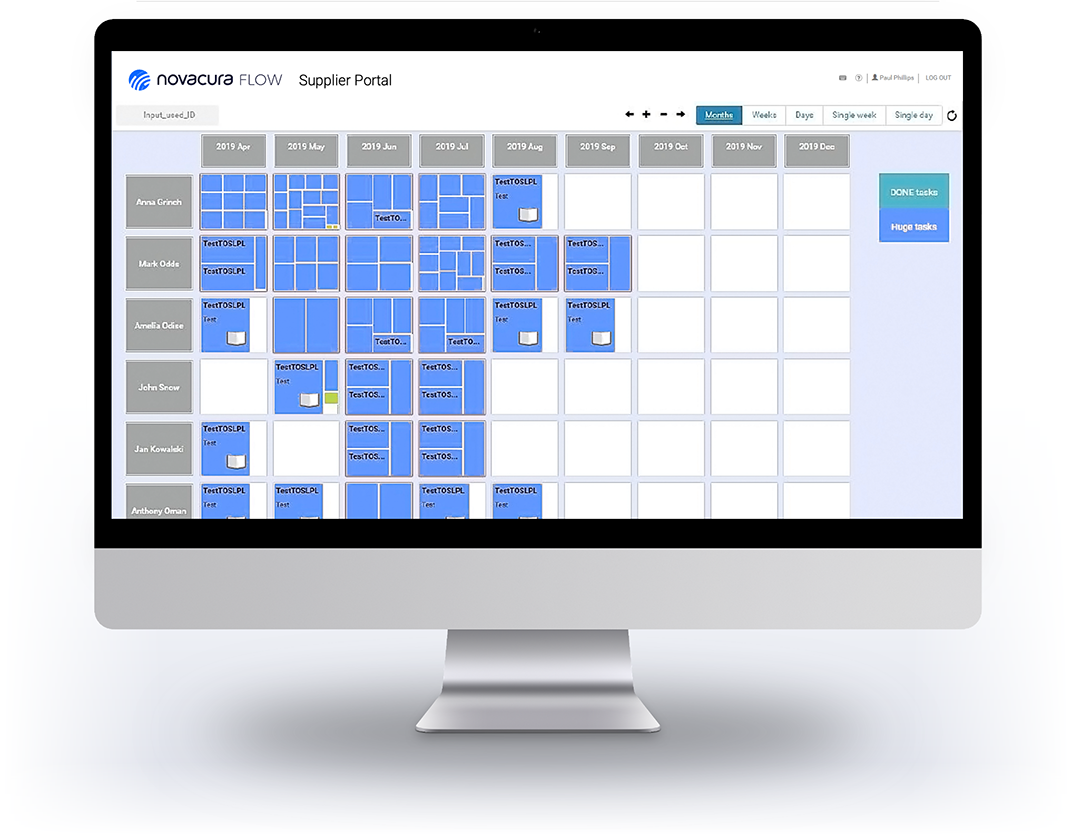
02. Connect internal logistics with the shop floor
Your internal logistics may use the same mobile application as your shop floor operators. Therefore, all the material delivery requests, material return requests or packaging return requests issued from the work center at the production line are immediately visible to logistics operators. And when logistics start delivery, production immediately gets a status update.

03. Optimize picking paths
In our warehouse solution (a complete mobile WMS), the operator shows picking lists in a mobile application. The solution optimizes the picking path based on the location, weight, further unload sequence, or even expiration date of particular goods. And – of course – the operators can use barcode scanners as their tool!
This ensures faster, more accurate order fulfillment while reducing human error. With real-time data synchronization, the manufacturing app keeps inventory levels up-to-date, streamlining warehouse operations effortlessly.
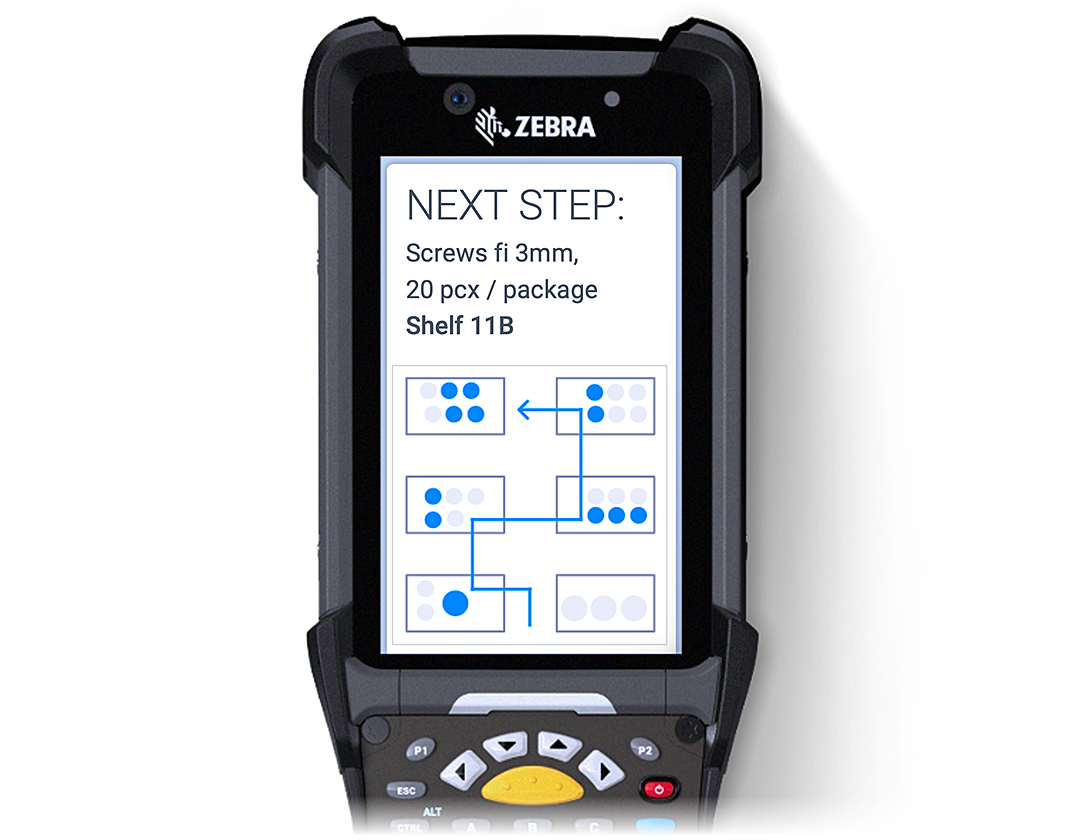
04. Work mobile and report every operation
Thanks to the mobile shop floor application, operators get all the details about their work orders. And they get it immediately after the plan has been updated (online). Operators report their work, and the information is also sent directly to the ERP / planning system.
They not only report their direct tasks, but they can also report downtime, call for material supply, request packages, report scrap or call for maintenance. Thanks to that, managers have complete online insight into the operations and can react quickly and optimize OEE regularly. This solution is an essential component of modern software for manufacturing industries, enabling real-time data flow and improved operational efficiency.
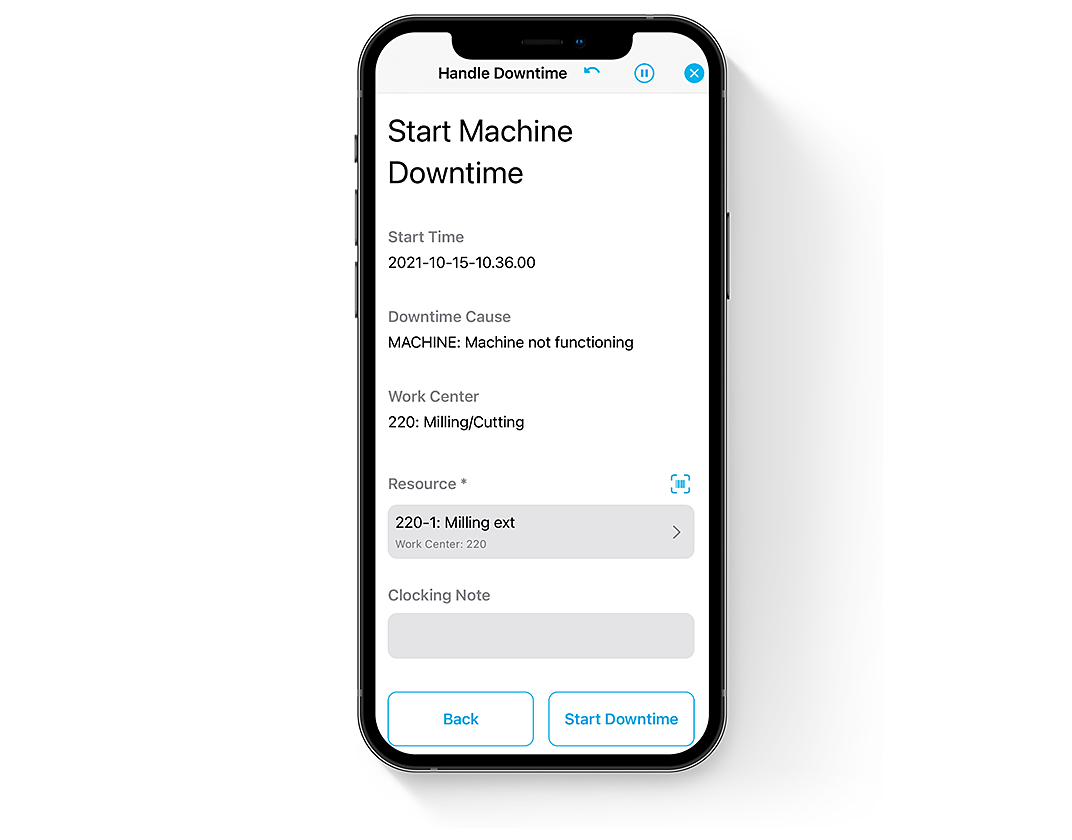
05. Incorporate maintenance and reduce downtime
In Novacura Flow, Production Management and Maintenance Management are seamlessly integrated into the same cloud manufacturing software solution. The service team can fit maintenance activities into production plans, even if they change every hour. Moreover, whenever downtime is identified on the shop floor, the maintenance team can be automatically notified in the mobile application and start activities before the machine operator starts calling for help. That will help reduce MTW.
06. Track actual data & optimize the entire process
With the Novacura Flow applications, Production efficiency can be precisely measured – you can gather information from all departments that use mobile applications and read them directly from your devices.
Novacura Flow is equipped with different industrial connectors (BLE, OPC-UA, PLC, RFID) which allow it to read other online information from other devices and machines.
And a lot more…
Let us show you our complete package of applications dedicated to supporting manufacturing companies!
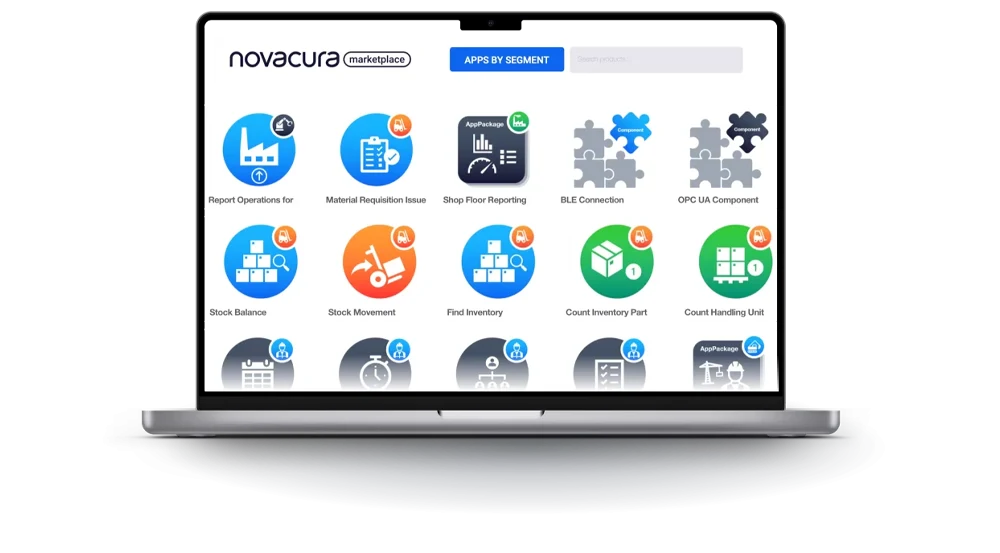
Manufacturing software solutions and supported areas:
Below we summarize the list of areas supported by our package of mobile applications for manufacturing companies:
01
Maintenance
- Maintenance tasks planning – Integration with production plans
- Mobile Work orders for maintenance (preventive & reactive)
- Tools management
- Spare parts management
- Maintenance subcontractors management (incl. financial settlements)
02
Shop floor operations
- Mobile shop orders processing
- Reporting (Time, Material, Scrap etc.)
- Logistics requests (material requisitions, returns, package requisitions)
- Downtime reporting
- Defects reporting
- Maintenance calls
- Staff management
03
Internal logistics
- Material delivery (JIT, up to particular production sequence)
- Different picking strategies support (FIFO, FEFO, LIFO)
- Warehouse <> Shop floor transportation management
- External inventory usage optimization
- Material returns management (from production)
- Finished goods transportation
04
Inventory operations
- Material storage (material moves, handling unit management, traceability)
- On-the-fly Inventory counting support
- Picking paths optimization
- Outdated materials / Scrap management
- Barcode labels management
- Full support for barcode scanners
05
Production Planning and Supervision
- Long-term and short-term production planning
- Real-time updates to daily production plans
- Support for BOM-based and configure-to-order production
- KPI dashboards and shop floor visual screens
- OEE evaluation and defects traceability
- Material and supplier performance analysis
- Continuous improvement with low-code tools
06
Delivery & Shipment management
- Stock level management based on production plans
- Delivery planning & management
- Financial settlements with suppliers and customers
- Finished goods inventory management
- Shipment planning
- Transportation management
- Returnable packaging management
Our Software Platform:
Interface optimized for thousands of operations per day
Our applications run on a sophisticated software platform – Novacura Flow. One of the key foundations of this platform is to run on every device – from barcode scanners, via mobile phones and tablets, to desktop workstations equipped with large screens.
But we are not just another SaaS software that offers that. We have optimized our user interface for users that work on a shop floor, in a warehouse, or in the field. We know that every “click” matters for these people because they run 1000+ operations a day!
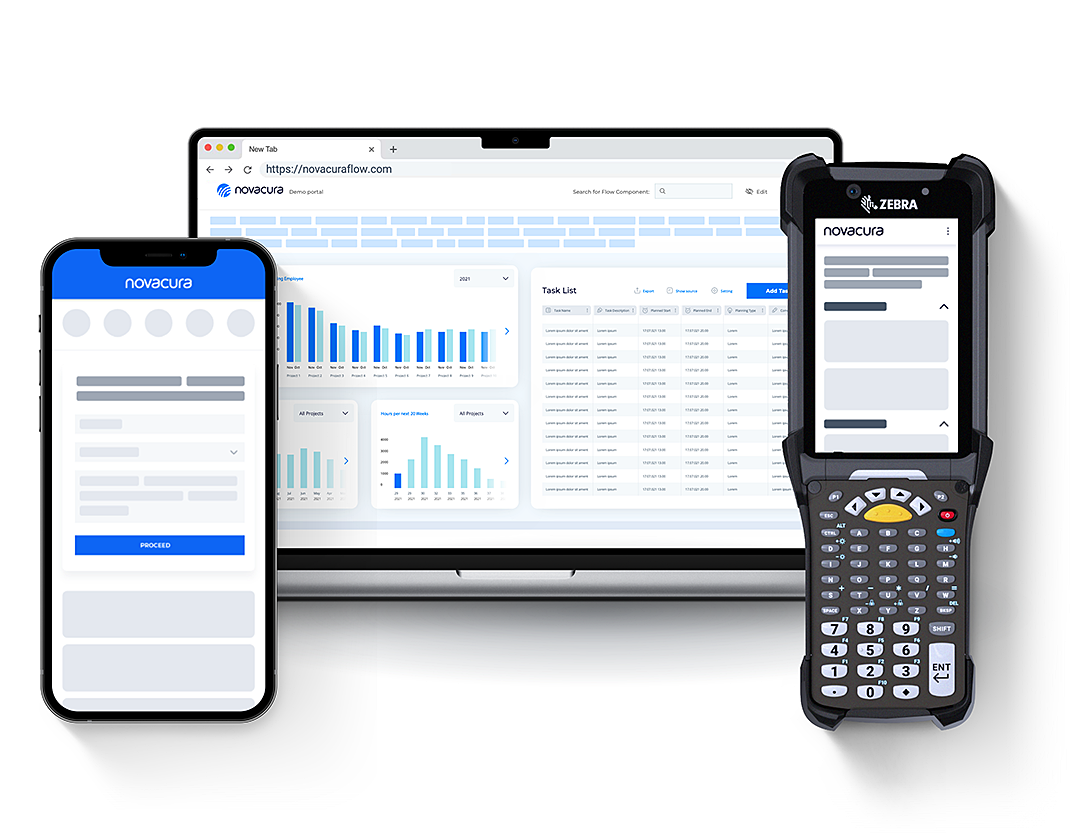
Ready for changes thanks to its low-code core!
Every company is different from the other. You might have specific processes and require unique features and we are ready for that! We created our applications for manufacturing based on the low-code platform.
Our applications are not hard-coded so our customers can modify them or clone them and create variants. And they can build their own applications. And thanks to the low-code engine they can create applications by drawing them like they draw a business process.
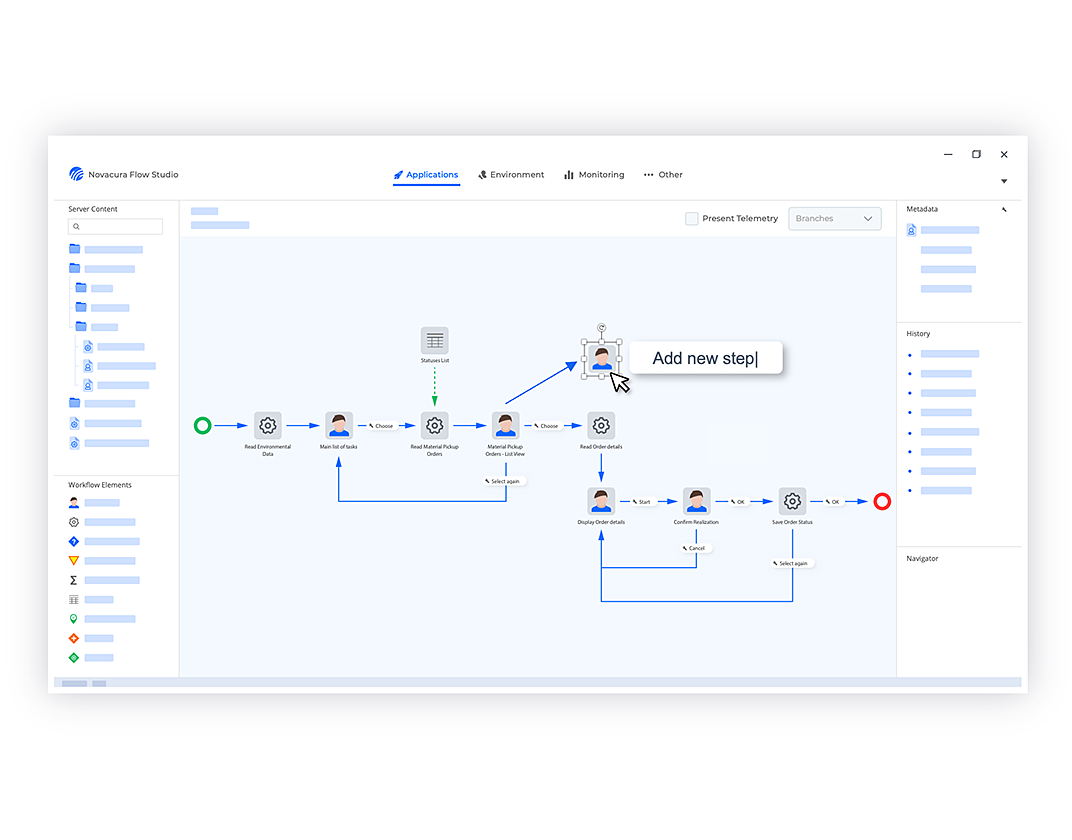
Integration with ERP. Deep integration!
Our low-code platform Novacura Flow and industry applications can play a vital role for a manufacturing company. But we are not forgetting about the ERP!
We treat the ERP system as a primary system – all the master data, operations and reported information is stored there. And everything that users do in Novacura is immediately visible in the ERP! It´s possible because our platform has specialized online connectors to ERP systems. You can think about Novacura Flow as an alternative, mobile and efficient user interface for your ERP. Thus, you can easily adopt Novacura Flow without changing the surrounding processes which can still run in your ERP!
The process is seamless and risk-free:
The implementation process takes less time than usual.
We have a solution that can be easily integrated with existing systems.
1. Mature methodology
A structured implementation methodology, divided into stages like initial requirements workshops and feasibility studies, ensures predictability and control. This approach helps businesses efficiently plan projects while understanding the cost of manufacturing software.
2. Years of experience
We have 17+ years of experience in Manufacturing. We have a library of ready-to-use applications which can be
presented to the customer and customized according to his needs.
3. Low-code platform
The Novacura Flow platform offers low-code flexibility, enabling rapid implementation and full customization. Every feature can be adjusted to meet specific requirements, making it a perfect fit for modern manufacturing environments.
4. Industrial connectors
A robust set of industrial connectors ensures seamless integration with ERP systems and other technologies. This eliminates connectivity challenges while optimizing manufacturing operations.
Our customers:
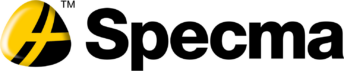

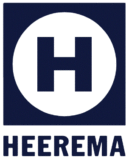
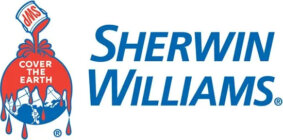
CONTACT OUR EXPERT:
Looking for personalized advice? Feel free to ask Fredrik about how Novacura can tailor solutions to your business. Fill out the form, and we’ll get back to you shortly!
Prefer email? Contact us here: info@novacura.com
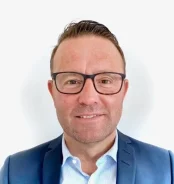