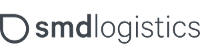
We had the pleasure of speaking with Herman Moodysson, Manager IT & Business Development at SMD Logistics, about their transition from the Merit Portal to Novacura Flow.
SMD Logistics serves as the essential intermediary connecting manufacturers with the Swedish market by distributing tobacco and tobacco-related items. Beyond tobacco, they also act as wholesalers for various high-demand consumer goods. SMD Logistics’ distribution infrastructure, guided by principles of security, quality, and sustainability, extends to 10,000 clients across Sweden and Norway.
In the interview presented to our readers, Herman Moodysson, IT Manager at SMD Logistics, shared insights into their transition from Merit Portal to Novacura Flow for logistics operations.
HIGHLIGHTS FROM THE INTERVIEW
The interview was performed on 2024-05-21, between:
- Herman Moodysson (HM) from SMD Logistics, and
- Łukasz Majer (LM), Business Solutions & Marketing Director at Novacura.
LM: Could you please introduce yourself, detailing your current role within your company and sharing some background information about yourself?
HM: Certainly. I’m employed as the IT Manager and Business Development professional at SMD Logistics. I’ve dedicated 13 years of service to the company, with my responsibilities centered around IT since the beginning. Earlier in my career I served as an IT Consultant at Intentia, a company now under Infor’s ownership, where I gained extensive experience with Infor M3.
LM: Could you provide us with an overview of your company, including the products/services offered, and target markets?
HM: SMD Logistics specializes in the transportation of high-value goods, predominantly tobacco products.
We are the logistics partner for all major tobacco companies in the Swedish market and to some extent in Norway. While we maintain our own fleet for the Greater Stockholm area, we rely on external transport companies for other regions.
LM: Could you share some key figures regarding your company’s operations?
HM: We currently have a workforce of over 200 employees.
Our main business is distribution of tobacco products and we serve the majority of retail outlets in Sweden, around 80% directly to point-of sale (POS) and the remaining 20% through wholesale operations.
Our clientele encompasses approximately 7 500 delivery points, including prominent chains such as ICA, Axfood, Reitan and Circle K, alongside independent retailers.
We also have a small but growing business acting as 3PL to e-commerce customers.
LM: Could you tell us something about what differentiates your business from the generic logistics operators?
HM: One thing is that we are acting as a logistics partner to different competing businesses, meaning competitive neutrality is fundamental to us.
Secondly, since we deliver tobacco products, our business must meet restrictive safety and compliance regulations.
LM: Thank you! Could you now provide an overview of your IT infrastructure, including the ERP system you use?
HM: As our main ERP system, we use Infor M3 13.4, on-premises. It is supplemented by MEC (M3 Enterprise Collaborator) engine for integration management.
Since our strategy is to be a fully digital company, we use several systems to be able to process 98% of our customer orders digitally. We use an EDI platform and we also have a web-based B2B portal to cooperate with our customers.
We also use our internally developed “Track & Traces” solution to comply with EU directive that is applicable for all companies delivering tobacco products (Tobacco Products Directive 2014/40/EU, 2019).
We also use Merit Portal Claims for claims management.
And – last but not least – we use Novacura Flow to support all the warehouse operations.
LM: Talking about Novacura Flow – could you please recall how this cooperation with Novacura started?
HM: Yes. It all started in 2018. At that time, we were still using the Merit Portal Supply Chain to support our core processes (logistics). Due to the fact, that our business would soon be affected by the “Tobacco Products Directive 2014/40/EU” and especially the “Track & Trace” regulation coming in 2019, we were analysing various options for providing necessary reporting to be compliant with these legal requirements.
We quickly realized that Merit Portal did not have the integration capabilities that we needed and therefore started looking for alternatives and this is how we found Novacura Flow.
At that time, I was a leader of the Project Management team responsible for implementing Novacura Flow.
After a quick analysis, we understood, that Novacura Flow can solve our problems if we decide to replace the Merit Portal with logistic applications built in Novacura Flow. We first started with core operational processes. In Novacura Flow, when we pick and pack orders, we not only update Infor M3, but also transmit data to our internal Track & Trace solution, which subsequently transmits data to the external repository.
LM: What was your Merit Portal replacement strategy? Did you completely replace it one day, or it was more like a step-by-step approach?
HM: Definitely the latter. Due to the fact, that the Merit Portal Supply Chain was used in many areas and processes, we didn’t plan the revolution and a sudden replacement. Instead of that, we decided to replace it with Novacura Flow in a gradual way, where we migrate functionalities in portions, over a longer period of time.
It was doable thanks to the fact, that Novacura Flow is deeply integrated with our Infor M3 solution, so all the information processed and prepared by Novacura Flow was always stored in the Infor M3 database. As a consequence, the effects of Novacura Flow operations were always visible for modules of the Merit Portal that were still in use at that time. This unique characteristic of Novacura Flow actually enabled us to do it that way and it was a very convenient strategy for us because we had limited resources.
LM: I guess, it was also a less stressful strategy?
HM: Yes – we eliminated a lot of risks typically connected with projects, where one day you completely replace one system with another. Our step-by-step approach was not only less stressful for IT , but also for the end-users!
LM: Now that you’ve been using Novacura Flow for a few years. Having that broader perspective, could you summarize the benefits of using it over the Merit Portal solution?
HM: I could highlight the main benefits in the following way:
- User Interface: The Merit Portal user interface appeared outdated. With Novacura Flow, you get modern-looking mobile applications for all platforms, you can also use it in a web browser.
- Efficiency in use: Flow applications better reflect the real processes happening in the warehouse and it has a positive impact on the workflow efficiency or the warehouse operators.
- Flexibility: with Novacura Flow, we can literally change everything, add new features, implement additional conditions to protect the work quality, and adopt any new regulations. And we do that within days or weeks.
- Integration openness: as I mentioned before, the Merit Portal had limited integration capabilities and we couldn’t integrate it with the Track & Trace solution. In Novacura Flow, you can naturally integrate your solution with your ERP and any other systems.
Additionally, it streamlines the onboarding process for new employees and facilitates quick adjustments to enhance efficiency. It happens thanks to the fact, that Novacura Flow offers a very simple step-by-step user interface that guides the user through the process.
We also like Novacura Flow’s ability to implement the changes gradually. We test our changes in a limited environment, where new applications are used by a limited number of users (eg. at one picking station) at a time, before full implementation
I would also like to add one example here to present the efficiency. To meet the “Track & Trace” regulation requirements, we developed Novacura Flow apps in a way, where most of the data necessary for the Track & Trace solution is gathered “on the fly”, as people perform their regular tasks. The collection of data doesn’t require additional steps from the end users – it just happens in the background!
Furthermore, Novacura Flow is a future-proofing solution for our Infor Cloud migration.
LM: Speaking of which… Are you currently considering migrating to the Infor Cloud?
HM: Yes, we are moving in that direction. It’s part of our IT strategy, but it’s not a current project because we only recently upgraded to Infor M3 13.4 in September 2023.
LM: Did Novacura Flow help you transition from the previous Infor M3 version to 13.4?
HM: Yes, a lot! Previously, we had over 60 modifications within our Infor solution, which hindered smooth upgrades. On the journey toward 13.4 version, we decided to eliminate the vast majority of our modifications, to be prepared for future upgrades. One way of doing this was extending Infor M3 externally – by using low-code applications created in Novacura Flow as modification substitutes.
Novacura Flow was an important tool in reducing the number of 60 modifications to approximately 10 of them!
Currently, we employ Flow alongside MEC, though some modifications are still required in M3 as we prepare for the Cloud transition. We’ve transitioned from traditional SQL-based integrations to utilizing the REST API for future-proofing.
LM: I guess you still plan to use Novacura Flow after you finally migrate to Infor Cloud?
HM: That’s the plan! We know that Flow connector supports the latest Infor Cloud version so this should be doable without delays.
LM: At the end, I must ask about the future plans. Do you plan to expand Novacura Flow to other process areas, like office administration, procurement, or claims management?
HM: The answer is yes and no!
We definitely want to build more apps in Novacura Flow, because we see a very positive impact on our business – both in the efficiency and process quality areas.
But instead of focusing on other process areas (like administration or procurement), we plan to continue the improvement of our core logistic processes, where most of our operations and resources are involved. So each implemented change has immediately a big impact on our business!
In the future, when we start our Infor Cloud project, we will consider the replacement of the remaining Merit Portal module (Claims management) with dedicated Novacura Flow applications integrated with Infor M3 Cloud!
LM: Thank you for the interview!
HM: Thank you!
SUMMARY
In the interview, Herman Moodysson, discussed SMD Logistics transition from Merit Portal to Novacura Flow for logistics operations. They found Merit Portal limiting, especially for compliance with regulations like “Track & Trace”. Novacura Flow offered modern UI, improved efficiency, flexibility, and better integration capabilities. The transition was gradual, reducing stress and risks. Novacura Flow also aided their upgrade to Infor M3 13.4, minimizing modifications. Looking ahead, they plan to continue using Novacura Flow post-migration to Infor Cloud, focusing on core logistics processes.